L’analyse vibratoire est aujourd’hui une technique incontournable pour assurer la fiabilité des machines tournantes dans l’industrie. En permettant la détection précoce des défaillances, elle optimise la maintenance prédictive et réduit les coûts de maintenance. Mais comment fonctionne-t-elle concrètement ? Quels sont ses avantages et comment la mettre en œuvre efficacement ? Cet article répond à ces questions en détaillant les principes fondamentaux et les meilleures pratiques en matière d’analyse vibratoire.
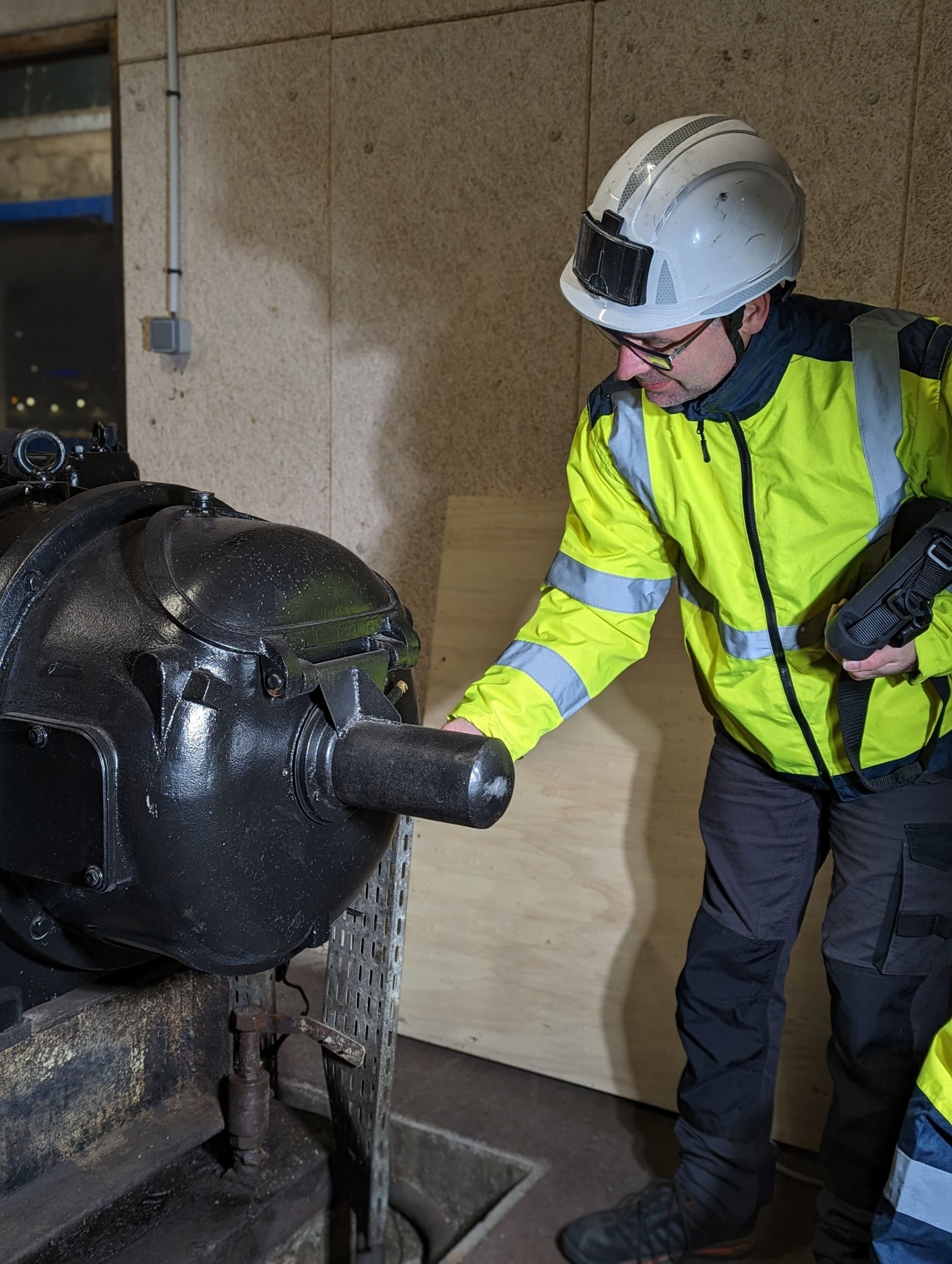
Sommaire
Qu’est-ce que l’analyse vibratoire ?
L’analyse vibratoire repose sur l’étude des vibrations émises par une machine en fonctionnement. Chaque équipement industriel possède une signature vibratoire propre, qui peut être modifiée par l’usure, les déséquilibres, les défauts de roulements ou encore les problèmes d’alignement. Grâce à des capteurs spécifiques (accéléromètres, capteurs de vitesse, capteurs de déplacement), il est possible de collecter des données vibratoires et de les analyser pour anticiper les pannes.
À lire aussi 💡Tout savoir sur l’analyse vibratoire
Méthodes d’analyse vibratoire
L’analyse vibratoire repose sur plusieurs approches complémentaires :
- Analyse temporelle : étude de l’évolution des vibrations dans le temps pour détecter des anomalies soudaines ou progressives.
- Analyse fréquentielle : identification des fréquences caractéristiques des défauts mécaniques via la transformation de Fourier (FFT).
- Analyse modale : évaluation des fréquences propres de la machine pour anticiper des phénomènes de résonance.
- Analyse des enveloppes spectrales : utilisée pour détecter les défauts naissants dans les roulements et engrenages en mettant en évidence des fréquences harmoniques spécifiques.
Pourquoi utiliser l’analyse vibratoire en maintenance prédictive ?
L’analyse vibratoire présente plusieurs avantages clés pour la maintenance des machines tournantes :
- Détection précoce des défaillances : Identification des anomalies avant qu’elles n’entraînent une panne.
- Optimisation des performances : Réduction des temps d’arrêt imprévus et augmentation de la disponibilité des équipements.
- Réduction des coûts de maintenance : Limitation des interventions curatives et amélioration de la planification des opérations de maintenance.
- Amélioration de la sécurité : Prévention des risques liés aux défaillances des équipements industriels.
- Conformité aux normes : Respect des standards tels que l’ISO 10816 qui définit les seuils acceptables de vibrations pour différentes classes de machines.
Mise en œuvre d’une stratégie d’analyse vibratoire
Choisir les bons capteurs
Le choix des capteurs est essentiel pour obtenir des mesures précises. Selon le type de machine et l’objectif de surveillance, il faudra opter pour :
- Accéléromètres : adaptés aux hautes fréquences et aux chocs.
- Capteurs de vitesse : plus sensibles aux basses fréquences et aux déséquilibres.
- Capteurs de déplacement : utilisés pour des mesures de faibles amplitudes.
- Techniques sans contact : telles que les capteurs laser pour mesurer les vibrations dans des environnements difficiles.
Collecte et interprétation des données
Les données vibratoires doivent être collectées à intervalles réguliers pour identifier d’éventuelles tendances. Des logiciels d’analyse avancés permettent de décomposer le signal vibratoire pour déterminer l’origine des anomalies.
L’analyse fréquentielle joue un rôle clé, notamment avec l’utilisation de spectres de vibrations et de cartes de tendances spectrales, qui permettent d’identifier des signatures vibratoires spécifiques à chaque type de défaut mécanique.
Actions correctives et maintenance conditionnelle
Une fois les anomalies identifiées, il est crucial de mettre en place des actions correctives telles que :
- Équilibrage des rotors : correction des déséquilibres dynamiques pour réduire les charges sur les roulements.
- Remplacement des roulements : intervention ciblée pour éviter une défaillance totale.
- Réalignement des axes : réduction des forces parasites qui accélèrent l’usure.
- Surveillance continue : intégration de capteurs connectés et d’outils de monitoring en temps réel.
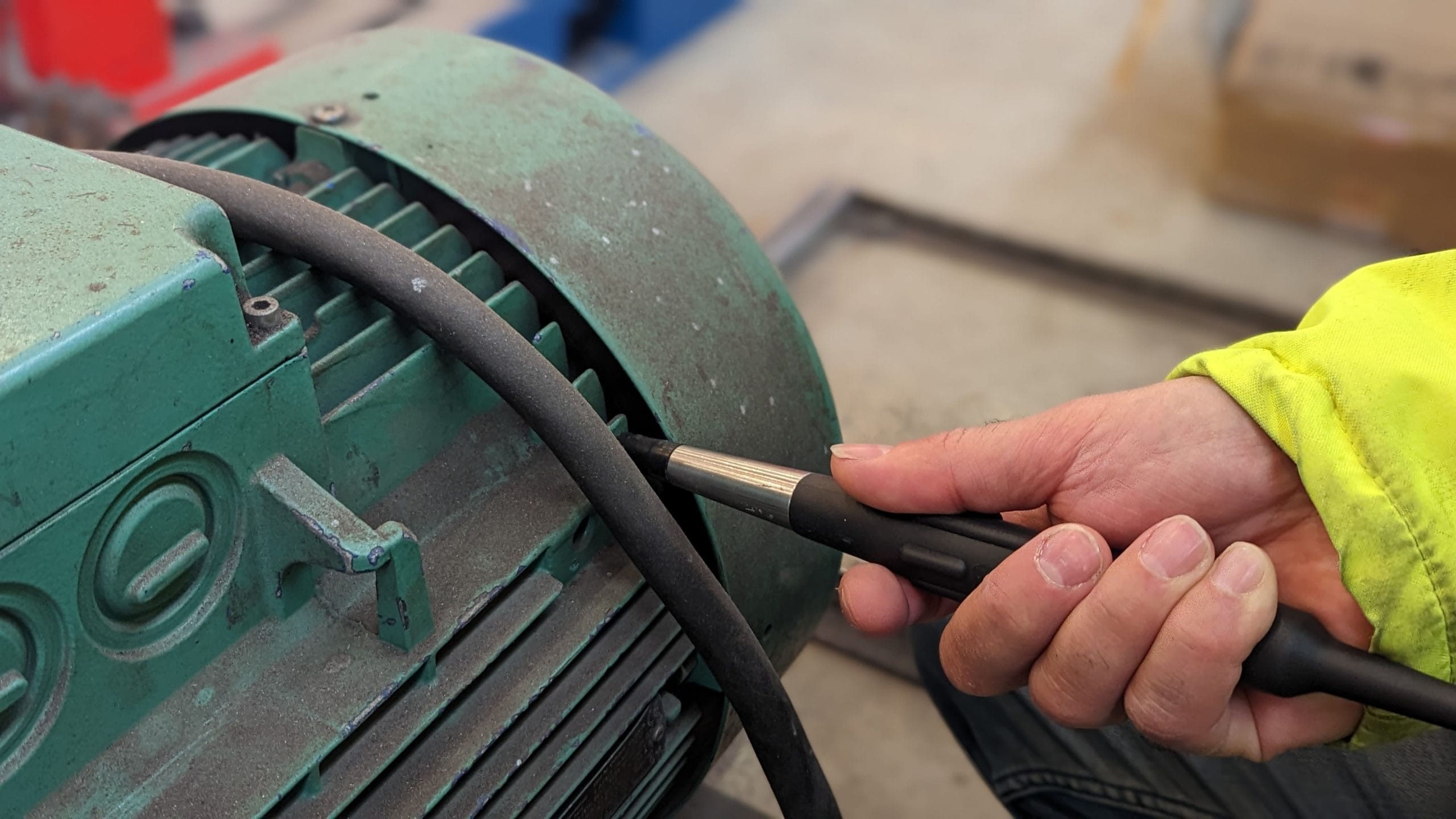
À lire aussi 💡 Comment effectuer une mesure vibratoire ?
Exemples d’application de l’analyse vibratoire
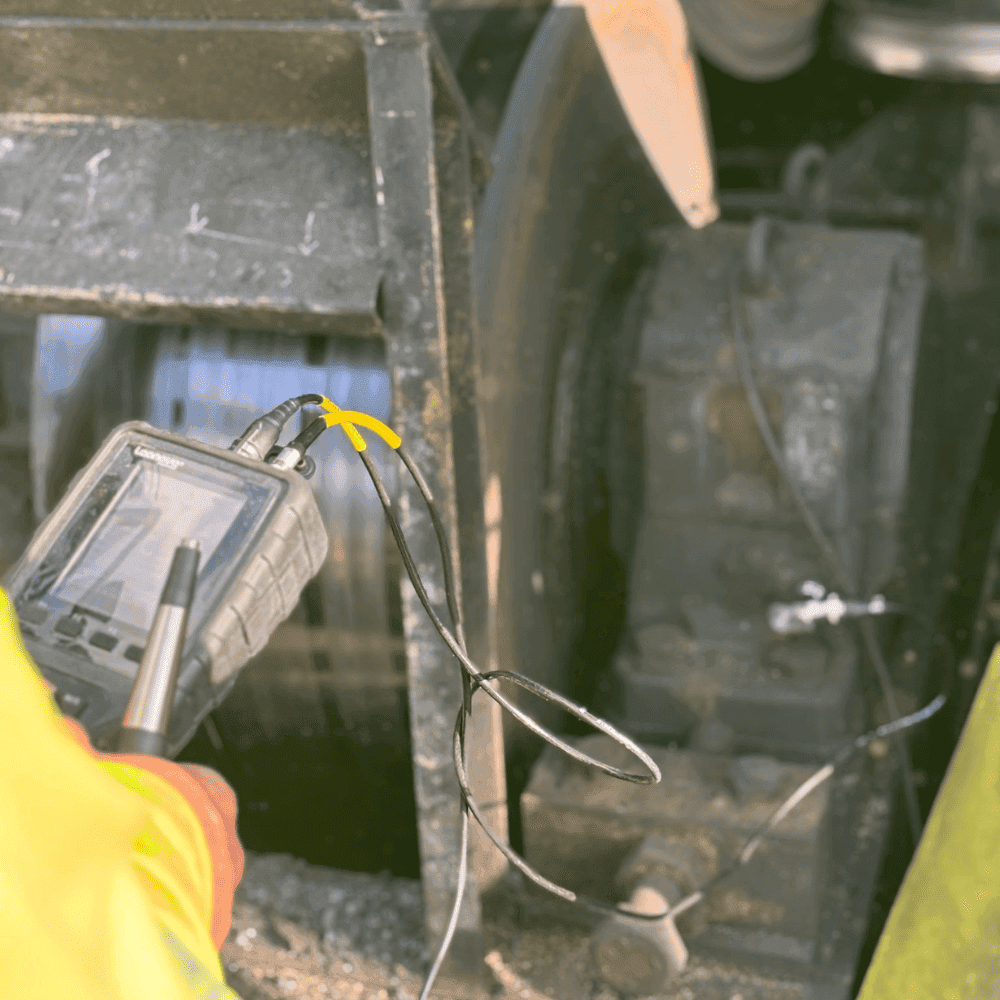
Une usine de papeterie à mis en place un système d’analyse vibratoire en continue au sein de sa strcuture, supervisé par l’entreprise ase-serem. Afin de surveiller et de prédéfinir les potentiels pannes sur la ligne de production.
Importance de la formation en analyse vibratoire
Pour une analyse vibratoire efficace, il est essentiel de former les techniciens et les ingénieurs à l’interprétation des données et à l’utilisation des logiciels d’analyse. Des certifications et formations spécialisées permettent d’acquérir les compétences nécessaires.
Conclusion.
L’analyse vibratoire est un outil indispensable pour la maintenance prédictive des machines tournantes. En détectant précocement les défaillances, elle contribue à l’optimisation des performances industrielles et à la réduction des coûts. Sa mise en œuvre repose sur une stratégie rigoureuse et une formation adaptée des professionnels.
Pour aller plus loin, explorez les solutions de surveillance avancée et formez-vous aux techniques de diagnostic vibratoire.
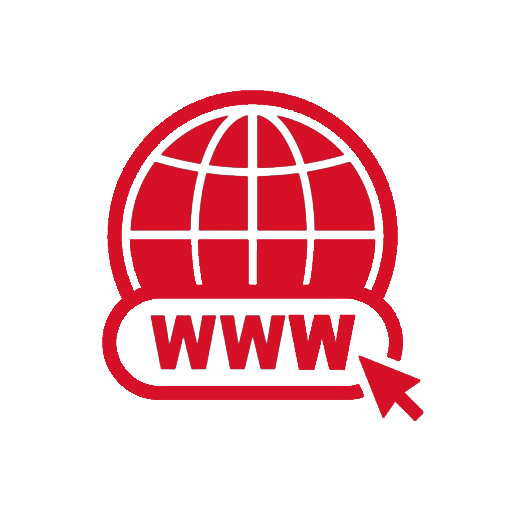
Découvrez notre offre de maintenance industrielle.
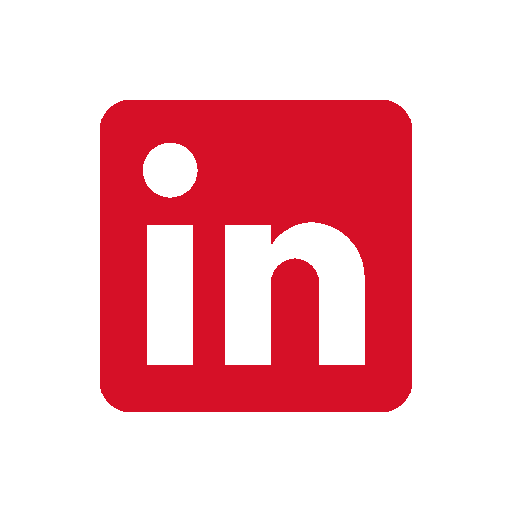
Découvrez l’actualité de notre atelier au quotidien via notre page LinkedIn !